
Ha oído hablar del Sistema 5S, o no. O has oído hablar de dos o tres de las cinco S. Hay algunos que dicen que hay seis S. La gente tiene todo tipo de versiones de esto, pero vamos a hablar de las cinco S, como un sistema completo que Toyota hizo famoso. Nuestro enfoque es lograr que aplique las Ss como un sistema 5S lo antes posible a nuestras necesidades específicas en nuestra industria de la construcción.
Este sistema fue creado por Ford y luego mejorado por Toyota. Ford lo llamó el sistema CANDO. CANDO es un acrónimo desarrollado por Henry Ford para hacer el área de trabajo más organizada y eficiente.
C = Limpiar
A = Arreglar
N = Orden
D = Disciplina
O= Mejora continua
El propósito del Sistema 5S es el mismo que su intención original. Nos centraremos en las mismas actividades. Usamos palabras que comienzan con la letra S. También veremos su aplicación en la construcción en lugar de la fabricación.
Los japoneses adoptaron el sistema CANDO y crearon su versión, llamada Sistema 5S, incorporando cinco palabras japonesas que comienzan con la letra "S". Hemos traducido las palabras japonesas a 5 palabras en inglés que comienzan con la letra "S".

La clave para recordar es que la mejora continua no es posible sin estándares. Los estándares nos permiten la capacidad de predecir resultados y nos dan una sensación de certeza. Estamos mejor equipados para predecir el futuro. Este punto de partida, establecer un estándar, es la base para la mejora.
Nuestro objetivo es que piense y utilice el Sistema 5S lo antes posible. Nos centraremos en la traducción al inglés de estas palabras japonesas. A veces, cuando las cosas se traducen, los significados pueden perderse en esa traducción. Hemos estado haciendo esto por suficiente tiempo y nos sentimos confiados y entendemos su intención y propósito. A veces verá la palabra individual barrer o brillar que representa la tercera S. Otras veces verá la frase poner en orden reemplazando la palabra enderezar por la segunda S. En principio, son lo mismo.
Las cinco palabras que usaremos para nuestros propósitos de capacitación son ordenar, enderezar, barrer, estandarizar y mantener. Las 5S comprenden un sistema, y el líder Lean las tendrá memorizadas y sabrá cómo aplicar sus principios y utilizarlos como un sistema completo. Este marco de comprensión les ayuda a entrar en su trabajo, oficina, almacén o fábrica y saber si las cosas están en el lugar correcto y cumplen con los estándares creados.
He oído decir que si no está utilizando 5S, no hay Lean en su lugar de trabajo. Wow, toda la afirmación! ¿Por qué alguien diría tal cosa?
Cuando practicamos los principios Lean y usamos el sistema 5S, hemos sentado las bases para la mejora continua. He dicho muchas veces que cualquiera puede limpiar un desastre, lo cual es mejor que vivir con un desastre. Sin embargo, hacerlo no es 5S. Podemos limpiar un desorden y arreglar las cosas ordenadamente, pero esto no es 5S. Hemos exhibido algunos atributos de 5S cuando limpiamos un desorden y, por lo tanto, pensamos que estamos haciendo 5S. Desafortunadamente, eso no es cierto. No es 5S hacer un trabajo de limpieza y guardar las cosas.
Un área, o sitio de trabajo, que tiene 5S aplicadas permite que todos vean lo que está dentro del estándar y lo que está fuera del estándar. Por lo tanto, la idea de mejoras continuas comienza en el momento en que tenemos un estándar existente. La mejora continua es pasar de un estándar al siguiente estándar a medida que avanzamos hacia la meta, eliminando cualquier desperdicio que veamos.
5S es la forma en que llegamos a este primer estándar y progresamos de un estándar al siguiente. Solo mediante la identificación de anomalías en el estándar; y las razones de estas anormalidades; ¿Podemos estabilizar y mejorar el proceso? Eliminar los ocho desperdicios e identificar cómo regresan a nuestras vidas nos permite hacer mejoras en un viaje sin fin hacia la perfección. 5S es el catalizador para comenzar este viaje.
Limpiar un desastre no es algo triste. Tiene sus méritos. Sin embargo, el conocimiento del Sistema 5S lo guiará hacia nuevas fronteras de eficiencia y mejora. Una mejora que no hubiera creído posible en el pasado.
Como empleados, nos damos cuenta de que somos los dueños de este sistema. Cuando esto sucede, se vuelve mucho más fácil de implementar. Cuando implementamos 5S, podemos exponer los desechos. Después de exponer los desechos, podemos ver los desechos. Entonces, al ver el desecho, podemos eliminar el desecho.
Los residuos pueden ser una anomalía, o una desviación, de nuestros estándares. Podemos traerlo de vuelta al estándar. A veces, esta anormalidad representa una mejor manera de hacer las cosas. Alguien ha encontrado una mejor manera y, por lo tanto, está ignorando el estándar. Cuando se observa esto, se puede mejorar el estándar. Esto conduce a un mejor flujo y a una mayor eficacia del sistema. El beneficio grande e inesperado que notamos es que hemos reducido nuestros costos al implementar este sistema. Desde la perspectiva de los trabajadores, hemos desarrollado la responsabilidad necesaria para la resolución disciplinada de problemas.
En nuestro taller de prefabricación, contratamos a un consultor Lean para que viniera y nos ayudara a obtener Lean. Lo primero que pidió George, incluso antes de venir a nuestro taller de prefabricación (prefabricados), fue una serie de videos que mostraban cómo fabricamos nuestros ensamblajes en la pared. Este fue un gran proceso, ya que también nos mostró cómo visualizar los desechos. Estos videos se convirtieron en la base de nuestro proceso de mejora. Representaban la condición actual de trabajo. En una breve semana de consultoría, George nos enseñó muchas cosas. El primero fue cómo implementar y ejecutar 5S como un sistema completo. Éramos un taller de prefabricación y, como la mayoría de los talleres, creíamos que éramos Lean simplemente porque éramos un taller de prefabricación.
Esto es muy parecido a muchas empresas de fabricación de todo el mundo que piensan que, debido a lo que hacen, son inherentemente Lean. Estábamos limpios y organizados; ¿Eso no significaba que éramos Lean? No, no lo hizo. George compartió rápidamente que tratar las 5S como actividades separadas fue un error. Pensar en ellos como un sistema completo nos daría resultados extraordinarios. Una vez que completamos una iteración de las 5S para todo el taller, las mejoras se hicieron evidentes. Nuestro pensamiento cambió en cuestión de días. Nuestra capacidad para realizar mejoras impactantes floreció.
Nuestra primera mejora notable fue la forma en que construimos nuestros ensamblajes en la pared. Un ensamblaje básico tiene una caja eléctrica de acero, un cable a tierra, un anillo de barro, un soporte, un conector y un cable MC conectado a él. Hay muchas versiones de esto, pero en promedio, descubrimos a través de las pruebas que nos llevó alrededor de doce minutos construir cada ensamblaje de principio a fin.

Después de realizar mejoras en todo este proceso, las construimos en menos de cinco minutos . Nuestro primer trabajo produciendo estos tuvo una cantidad de veintiséis mil. Completamos el trabajo e hicimos los cálculos. Ahorramos más de ciento cincuenta mil dólares solo en las mejoras. Recuerde, esto fue para el primer trabajo al que aplicamos este estándar. Eso fue hace cinco años. Los ahorros continúan hasta el día de hoy, aumentando a lo largo de los años. Seguimos encontrando más residuos que eliminar. Estamos acumulando los ahorros cada vez que vemos y erradicamos los desechos. 5S como sistema funciona y el tiempo dedicado a aprenderlo, implementarlo y mantenerlo bien vale cada centavo gastado para ponerlo en marcha. Esto no es nada comparado con la cantidad de ahorros que producirá en su tienda. Recibirá beneficios residuales al hacer 5S. Su almacén, lugar de trabajo, fábrica y oficina verán las mejoras y comenzarán a trabajar sistemáticamente en el "estilo 5S" para eliminar el desperdicio. La forma de utilizar a un consultor de manera inteligente es elegir un flujo de valor, como ensamblajes en la pared, y concentrarse en ese producto o servicio. Al reducir la mano de obra requerida a través de mejoras pequeñas e incrementales, verá grandes ganancias. Usamos a George durante una semana y nos enfocamos en todo nuestro taller de fabricación (fab) y en este producto. Aprendimos cómo mejorar usando un método de tormenta de intentos hace milagros. Probamos algo y, después de ejecutar algunos ensamblajes a través del proceso, volvemos a intentarlo. Construimos sobre lo que funciona y descartamos lo que no funciona. Hacer esto durante 3 horas y ejecutar quince experimentos únicos entusiasmó y motivó a nuestro equipo. Vieron lo fácil que era para George impulsar la estrategia de aprender mediante la experimentación y se hicieron cargo. Lo hicieron por su cuenta. Solo necesitaban ese empujón.
Prepara la mentalidad
Antes de comenzar con Sort, recuerde reservar tiempo para crear una visión y capacitación. Esto no es natural para aquellos en la construcción. No estamos preparados para estar en una habitación, hablando, durante medio día. No lo confundas con una pérdida de tiempo. Este es el tiempo de habilitación. Le permitirá entrar en el espacio de cabeza adecuado para hacer 5S. Crear una visión, con el aporte de todos, es invaluable. Desarrollar una comprensión del estado actual utilizando un mapa de valor es invaluable. Crear insatisfacción con el statu quo es invaluable.
El primer paso es crear la brecha entre donde estamos y donde queremos estar. El segundo paso es obtener una buena comprensión de la forma en que se hacen las cosas hoy. Siempre has hecho las cosas así. Independientemente de la razón, la comprensión de cómo se lleva a cabo el trabajo es fundamental. Finalmente, es hora de soñar. Tener un sueño y conseguir que la gente se sume a él es el punto de partida del Sistema 5S.
Recuerda cuando le compartí los videos antes de que llegara. Después de revisar esos videos, George compartió que podíamos tomar el 50% del tiempo de nuestro proceso de construcción de un ensamblaje. Esto es ridículo. Pero lo hicimos en una semana corta. Probamos que se podía hacer, luego mantuvimos las mejoras a través de la disciplina. Todos nos inscribimos en el aprendizaje y el aprendizaje comenzó. Estábamos preparados para hacer Lean al preparar nuestras mentes para aprender. Creamos un Sistema de Producción de Aprendizaje para nuestra empresa. Comenzó con algo simple, como 5S, y se amplió para enfocarse en la resolución de problemas para eliminar el desperdicio y desarrollar la competencia de nuestra gente en la resolución de problemas.
Una última palabra sobre la preparación para las 5S. Las empresas que están mejor preparadas están construyendo sistemas en torno a los valores de su empresa. Los valores de la empresa pueden incluir excelencia en seguridad, gratitud, aprecio, respeto, mejora continua, colaboración, y la lista continúa. ¿Dónde se encuentran las 5S? ¿Qué valores admite un sistema como 5S? La respuesta es todo lo anterior. Practicar 5S significa practicar los valores por los que su organización jura vivir. ¿No debería ser 5S el primer sistema que implemente en un esfuerzo por ser la mejor opción de creación de valor para sus clientes? ¡La respuesta simple es sí!
ACERCA DEL AUTOR.
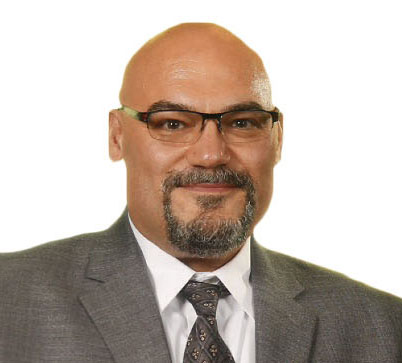
George Trachilis, P.Eng. vive en Canadá y consulta en todo el mundo. Comenzó su carrera en Motor Coach Industries en 1994, donde recibió capacitación Lean por parte de los mejores consultores en sistemas ERP, fabricación justo a tiempo y gestión de calidad total. Habiendo liderado el cambio durante más de 10 años, decidió iniciar su propia firma de consultoría en 2003. Creció hasta convertirse en una de las empresas de más rápido crecimiento de Canadá en 2006. George es un autor y entrenador ganador del premio de investigación Shingo. Es coautor de Lean Construction Leaders: A Trade Partner's Guide to Lean.
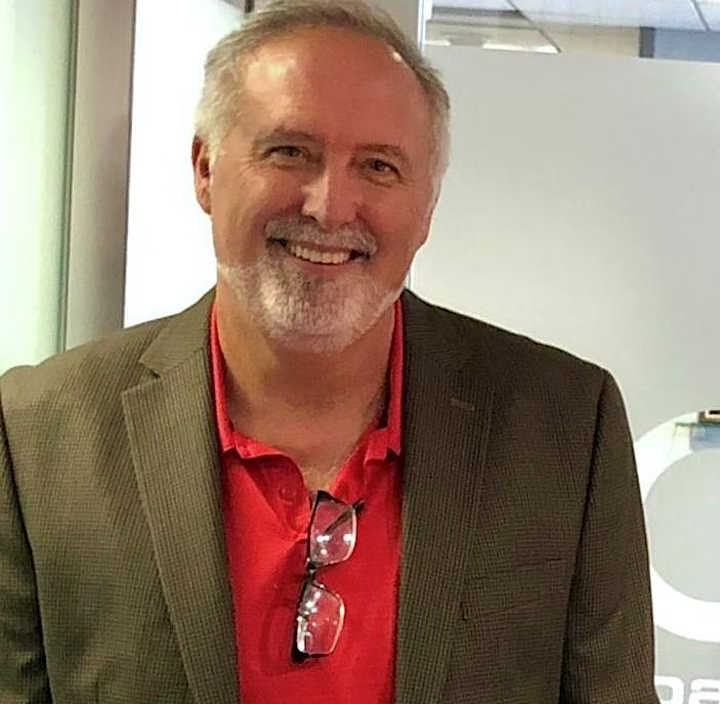
Perry es director ejecutivo Lean en Parsons Electric Company (PEC). El interés de Perry por la construcción comenzó con la tradición de construcción de su familia en los campos de la carpintería y la albañilería. Perry sirvió honorablemente en la Fuerza Aérea de los Estados Unidos. Después del servicio, pasó muchos años obteniendo títulos en la industria de la tecnología hasta que se unió a Parsons y comenzó su carrera en la construcción eléctrica, donde se desempeñó durante los últimos veinte años. Perry es instructor certificado del Lean Construction Institute (LCI), sirvió en la junta de educación de LCI y es instructor certificado del Lean Leadership Institute (LLI) de Jeff Liker.
TRANSCRIPCIÓN: Areli Álvarez Lean Construction México®
コメント