¿QUÉ ES SMED?
SMED (Single-Minute Exchange of Die) es un sistema para reducir drásticamente el tiempo necesario para completar los cambios de equipo. La esencia del sistema SMED es convertir tantos pasos de cambio como sea posible a «externos» (realizados mientras el equipo está en funcionamiento) y simplificar y optimizar los pasos restantes. El nombre Intercambio de troquel en un minuto proviene del objetivo de reducir los tiempos de cambio a un dígito «único» (es decir, menos de 10 minutos).
BENEFICIOS SMED
Un programa SMED exitoso tendrá los siguientes beneficios:
Menor costo de fabricación: cambios más rápidos significan menos tiempo de inactividad del equipo
Tamaños de lote más pequeños: cambios más rápidos permiten cambios de producto más frecuentes
Capacidad de respuesta mejorada a la demanda del cliente: los tamaños de lote más pequeños permiten una programación más flexible
Niveles de inventario más bajos: los tamaños de lote más pequeños dan como resultado niveles de inventario más bajos
Arranques más suaves: los procesos de cambio estandarizados mejoran la consistencia y la calidad
FUNDAMENTOS DE SMED
SMED fue desarrollado por Shigeo Shingo, un ingeniero industrial japonés que tuvo un éxito extraordinario al ayudar a las empresas a reducir drásticamente sus tiempos de cambio. Su trabajo pionero condujo a reducciones documentadas en los tiempos de cambio de un promedio del 94% (por ejemplo, de 90 minutos a menos de 5 minutos) en una amplia gama de empresas.
Los tiempos de cambio que mejoran en un factor de 20 pueden ser difíciles de imaginar, pero considere el ejemplo simple de cambiar un neumático:
Para muchas personas, cambiar un solo neumático puede llevar fácilmente 15 minutos.
Para un equipo de boxes de NASCAR, cambiar cuatro neumáticos toma menos de 15 segundos.
Muchas técnicas utilizadas por los equipos de boxes de NASCAR (realizar tantos pasos como sea posible antes de que comience la parada en boxes; utilizar un equipo coordinado para realizar varios pasos en paralelo; crear un proceso estandarizado y altamente optimizado) también se utilizan en SMED. De hecho, el viaje de un cambio de neumático de 15 minutos a un cambio de neumático de 15 segundos puede considerarse un viaje SMED.
En SMED, los cambios se componen de pasos que se denominan «elementos». Hay dos tipos de elementos:
Elementos internos: elementos que se deben completar mientras el equipo está parado
Elementos externos: elementos que se pueden completar mientras el equipo está en funcionamiento
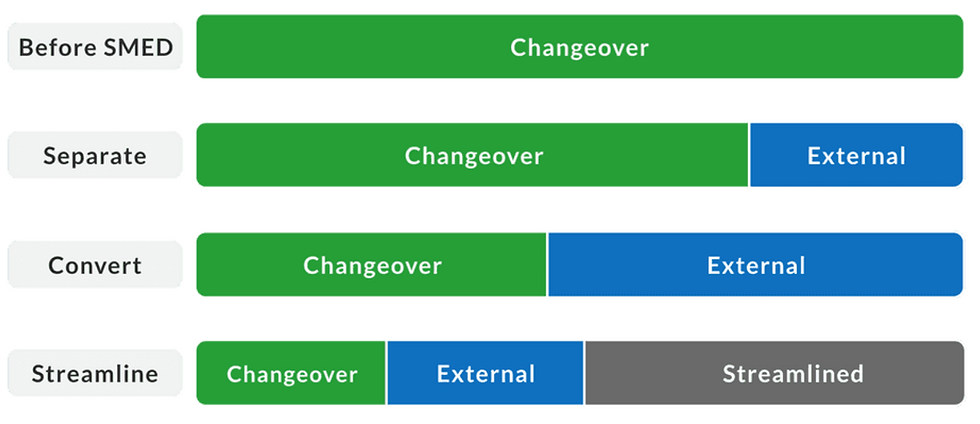
El proceso SMED se enfoca en hacer que tantos elementos como sea posible sean externos y simplificar y agilizar todos los elementos.
El sistema SMED tiene tres fases principales, como se muestra arriba. Estas fases se realizan en secuencia y la secuencia completa se puede iterar (repetir).
EJEMPLO DE SMED
Una excelente manera de aprender más sobre SMED es recorrer un ejemplo de implementación. Esta sección proporciona una hoja de ruta paso a paso para una implementación SMED simple y práctica.
Antes de empezar
Prácticamente todas las empresas de fabricación que realizan cambios de formato pueden beneficiarse de SMED. Sin embargo, eso no significa que SMED deba ser la primera prioridad. En el mundo real, las empresas tienen recursos finitos, y esos recursos deben dirigirse hacia donde generarán el mejor rendimiento.
Entonces, ¿cuál debería ser la primera prioridad? Para la mayoría de las empresas, la primera prioridad debe ser garantizar que exista una comprensión clara de dónde se está perdiendo el tiempo productivo y que las decisiones sobre las iniciativas de mejora se tomen en base a datos duros. Eso significa poner en marcha un sistema para recopilar y analizar datos de rendimiento de fabricación.
El «estándar de oro» de facto para los datos de rendimiento de fabricación es medir la OEE (eficacia general del equipo) con un desglose adicional de las categorías de pérdidas de OEE en las seis grandes pérdidas y un desglose detallado de las pérdidas de disponibilidad de OEE en códigos de motivo de tiempo de inactividad (incluidos los códigos para el seguimiento del cambio hora).
Una vez que se haya implementado un sistema para medir el rendimiento de fabricación, recopile datos durante al menos dos semanas para obtener una imagen clara de dónde se está perdiendo el tiempo productivo.

Paso uno: identificar el área piloto
En este paso, se selecciona el área objetivo para el programa piloto SMED. El equipo ideal tendrá las siguientes características:
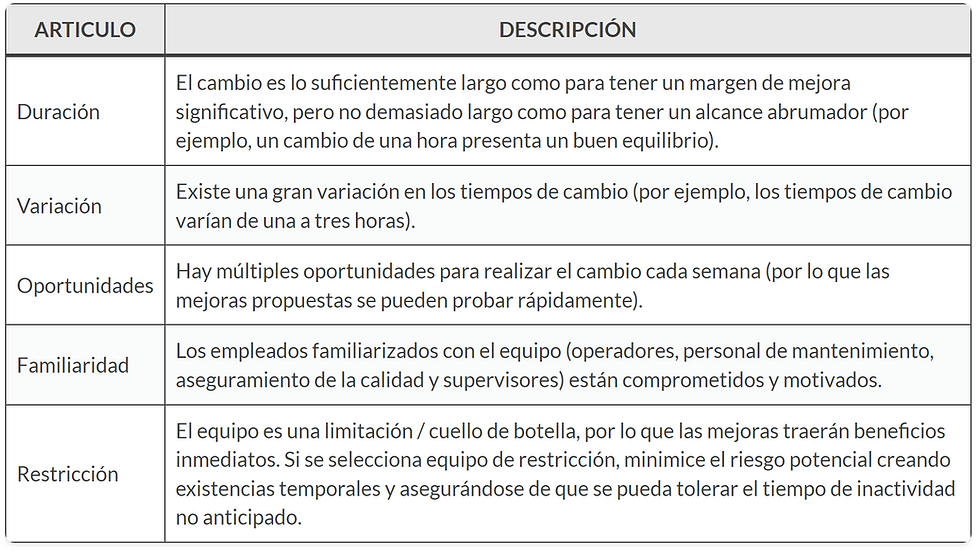
Con el fin de crear una amplia base de apoyo para el proyecto SMED, incluya el espectro completo de empleados asociados en el proceso de selección y trabaje duro para crear un consenso dentro del equipo en cuanto a la elección del equipo objetivo.
Una vez que se ha seleccionado el equipo de destino, registre un tiempo de referencia para el cambio. El tiempo de cambio debe medirse como el tiempo entre la producción de la última pieza buena (a velocidad máxima) y la producción de la primera pieza buena (a velocidad máxima). Sea consciente del «efecto Hawthorne»; Los tiempos de cambio pueden mejorar temporalmente como resultado simple de observar el proceso. Cuando sea posible, utilice datos anteriores para establecer la línea base del tiempo de cambio.
Paso dos: identificar los elementos
En este paso, el equipo trabaja en conjunto para identificar todos los elementos del cambio. La forma más eficaz de hacer esto es grabar en video todo el cambio y luego trabajar desde la cinta de video para crear una lista ordenada de elementos, cada uno de los cuales incluye:
Descripción: qué trabajo se realiza
Coste en el tiempo: cuánto tarda el elemento en completarse
Algunos consejos útiles para este paso:

El resultado de este paso debe ser una lista completa de elementos de cambio, cada uno con una descripción y un “costo” de tiempo.
Paso tres: elementos externos separados
En este paso, los elementos del proceso de cambio que se pueden realizar con poco o ningún cambio mientras el equipo está en funcionamiento se identifican y se mueven «externos» al cambio (es decir, se realizan antes o después del cambio). No es inusual que los tiempos de cambio se reduzcan casi a la mitad con este solo paso.
Para cada elemento, el equipo debe hacer la siguiente pregunta: ¿Se puede completar este elemento, como se realiza actualmente o con un cambio mínimo, mientras el equipo está en funcionamiento?
Si la respuesta es sí, categorice el elemento como externo y muévalo antes o después del cambio, según corresponda.
Ejemplos de elementos candidatos para dicho tratamiento incluyen:

El resultado de este paso debe ser una lista actualizada de elementos de cambio, dividida en tres partes: elementos externos (antes del cambio), elementos internos (durante el cambio) y elementos externos (después del cambio).
Paso cuatro: convierta elementos internos en externos
En este paso, se examina cuidadosamente el proceso de cambio actual, con el objetivo de convertir tantos elementos internos en externos como sea posible.
Para cada elemento interno, el equipo debe hacer las siguientes preguntas: Si hubiera una manera de hacer que este elemento sea externo, ¿cuál sería? ¿Cómo podríamos hacerlo?
Esto dará como resultado una lista de elementos que son candidatos para futuras acciones. Esta lista debe tener prioridad para que se actúe primero sobre los candidatos más prometedores. Básicamente, esto se reduce a realizar un análisis de costo / beneficio para cada elemento candidato:
Costo medido por los materiales y la mano de obra necesarios para realizar los cambios necesarios.
Beneficio medido por el tiempo que se eliminará del cambio.
Una vez que se ha priorizado la lista, se puede comenzar a realizar los cambios necesarios.
Ejemplos de técnicas que se pueden utilizar para convertir elementos internos en externos son:

El resultado de este paso debe ser una lista actualizada de elementos de cambio, con menos elementos internos y elementos externos adicionales (realizados antes o después del cambio).
Paso cinco: simplificar los elementos restantes
En este paso, se revisan los elementos restantes con miras a racionalizar y simplificar para que se puedan completar en menos tiempo. Se debe dar prioridad a los elementos internos para apoyar el objetivo principal de acortar el tiempo de cambio.
Para cada elemento, el equipo debe hacer las siguientes preguntas: ¿Cómo se puede completar este elemento en menos tiempo? ¿Cómo podemos simplificar este elemento?
Como en el paso anterior, se debe utilizar un análisis simple de costo / beneficio para priorizar la acción sobre los elementos.
Ejemplos de técnicas que se pueden utilizar para optimizar elementos son:

El resultado de este paso debe ser un conjunto de instrucciones de trabajo actualizadas para el cambio (es decir, crear Trabajo estandarizado) y un tiempo de cambio significativamente más rápido.
ACELERAR EL PROGRESO
Al implementar SMED, es útil reconocer que hay dos categorías amplias de mejora:
Humano: logrado a través de la preparación y la organización.
Técnico: logrado a través de la ingeniería.
La experiencia ha enseñado que los elementos humanos suelen ser mucho más rápidos y menos costosos de mejorar que los elementos técnicos. En otras palabras, las victorias rápidas suelen estar relacionadas con los elementos humanos. Evite la tentación, especialmente con equipos técnicamente competentes, de concentrarse demasiado en los elementos técnicos. En cambio, concéntrate primero en los elementos humanos.
El siguiente cuadro ilustra este principio, mostrando ejemplos de áreas de oportunidad para proyectos SMED.
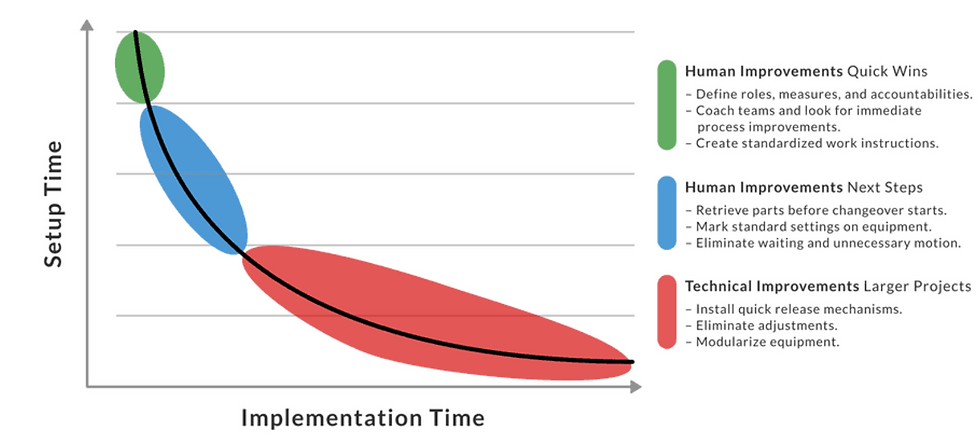
ACERCA DEL AUTOR. Lara Ortega
TRANSCRIPCIÓN: Areli Álvarez Lean Construction México®
Commentaires